Introduction
TIG (Tungsten Inert Gas) welding, also known as Gas Tungsten Arc Welding (GTAW), is a precision welding process widely used in industries requiring high-quality, clean welds. It is favored for its ability to create strong, visually appealing welds with excellent control over heat and material fusion. While TIG welding demands more skill than MIG or stick welding, it offers superior results for thin metals, aluminum, stainless steel, and exotic alloys.
What is TIG Welding?
TIG welding uses a non-consumable tungsten electrode to create an electric arc that melts the base metal. A separate filler rod is often used, but in some cases, metals can be fused without filler (autogenous welding). The weld pool is shielded by an inert gas, typically argon, to prevent contamination from atmospheric gases like oxygen and nitrogen.
Advantages of TIG Welding:
- Precision and Control – Allows fine control over the weld pool and heat input.
- Stronger, Cleaner Welds – Produces high-quality welds with minimal spatter and slag.
- Versatile – Can weld various metals, including aluminum, titanium, and stainless steel.
- No Need for Flux or Spatter Cleanup – The inert gas shielding eliminates the need for flux, reducing contamination.
Essential Equipment for TIG Welding
Before you begin TIG welding, it’s crucial to have the proper equipment:
- TIG Welder
A dedicated TIG welding machine provides adjustable amperage control, high-frequency start options, and AC/DC capabilities for different materials.
✅ Key Features to Look For:
- AC/DC Output – AC is required for aluminum; DC for steel and stainless steel.
- High-Frequency Start – Provides a non-contact arc initiation, preventing tungsten contamination.
- Foot Pedal or Finger Control – Allows precise amperage adjustment while welding.
- Pulse Function (Optional) – Helps control heat input on thin metals.
📌 Recommended TIG Welders:
- Miller Diversion 180
- Lincoln Electric Square Wave TIG 200
- Everlast PowerTIG 210EXT
- Tungsten Electrodes
TIG welding requires tungsten electrodes, which vary based on the material being welded:
- Pure Tungsten (Green) – Used for AC aluminum welding.
- 2% Thoriated (Red) – Most common for DC welding of steel and stainless steel.
- 2% Lanthanated (Blue) – Versatile and long-lasting for AC/DC applications.
📏 Electrode Size Guide:
- 1.6mm (1/16”) – Best for thin materials (under 3mm).
- 2.4mm (3/32”) – Most versatile for general welding.
- 3.2mm (1/8”) – Used for thicker metals (over 6mm).
- Shielding Gas & Flow Regulator
TIG welding requires an inert gas for shielding:
- 100% Argon – Best for most TIG welding applications.
- Argon/Helium Mix – Used for deeper penetration on thick metals.
🔧 Gas Flow Rate: 15–20 CFH (cubic feet per hour) for effective shielding.
- Filler Rods
Choosing the right filler metal is crucial for strong, durable welds:
- ER70S-2 – For mild steel.
- ER308L – For stainless steel.
- ER4043 or ER5356 – For aluminum.
📏 Filler Rod Thickness Guide:
- 1.6mm (1/16”) – For thin metals.
- 2.4mm (3/32”) – General-purpose welding.
- 3.2mm (1/8”) – For thick materials.
- TIG Torch & Consumables
The TIG torch directs the arc and shielding gas. It includes:
- Collet & Collet Body – Holds the tungsten electrode.
- Ceramic Nozzle – Controls gas coverage.
- Back Cap – Secures the tungsten in place.
- Ground Clamp
A solid ground connection is essential for a stable arc. Ensure:
- Clean contact points – Remove rust, paint, or oxidation before attaching.
- Strong clamp pressure – Prevents arc instability.
- Welding Helmet & Protective Gear
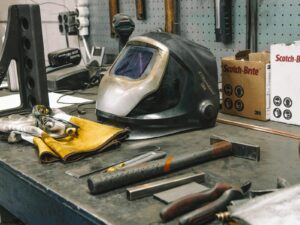
TIG welding emits intense light and heat, requiring proper safety gear:
- Auto-darkening welding helmet – Adjustable shade (#9–#13 for TIG welding).
- High-quality leather gloves – Provides dexterity while protecting against heat.
- Cotton or leather welding jacket – Prevents burns from UV exposure.
- Work Surface & Clamps
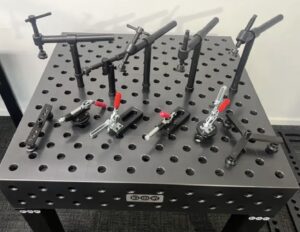
A stable work environment ensures better weld quality:
- Metal welding table – Conducts electricity efficiently.
- C-clamps or magnetic clamps – Holds the workpiece securely.
TIG Welding Techniques for Beginners
- Torch Angle & Travel Speed
- Hold the torch at a 10-15° angle.
- Move steadily to avoid overheating and warping.
- Puddle Control & Dabbing
- Maintain a consistent weld pool.
- Dip the filler rod smoothly into the puddle without excessive movement.
- Weaving & Stringer Beads
- Use stringer beads for precision welding.
- A slight weaving motion can help cover wider joints.
Common Mistakes & How to Avoid Them
- Contaminated Tungsten
- Always keep tungsten clean and sharpened.
- If it touches the puddle, regrind before continuing.
- Too Much or Too Little Heat
- Adjust amperage carefully based on material thickness.
- Use a foot pedal to fine-tune heat input.
- Poor Shielding Gas Coverage
- Set gas flow to 15-20 CFH.
- Check for leaks in hoses and fittings.
Practice Exercises for Beginners
- Straight Line Beads – Run beads on scrap metal to practice arc stability.
- Lap Joints & T-Joints – Common in structural welding.
- Corner Welds – Useful for fabricating enclosures and frames.
Conclusion
TIG welding is a highly precise and versatile process used for high-quality welds. While it requires practice and patience, mastering TIG welding can open doors to advanced fabrication and repair work. Start with the right equipment, focus on technique, and refine your skills through hands-on experience.